Acoustic wall panels are essential for improving sound quality and reducing noise in various spaces, from residential homes to corporate offices. But have you ever wondered how these panels are made? In this article, we’ll take you behind the scenes of the manufacturing process, from raw materials to the finished product.
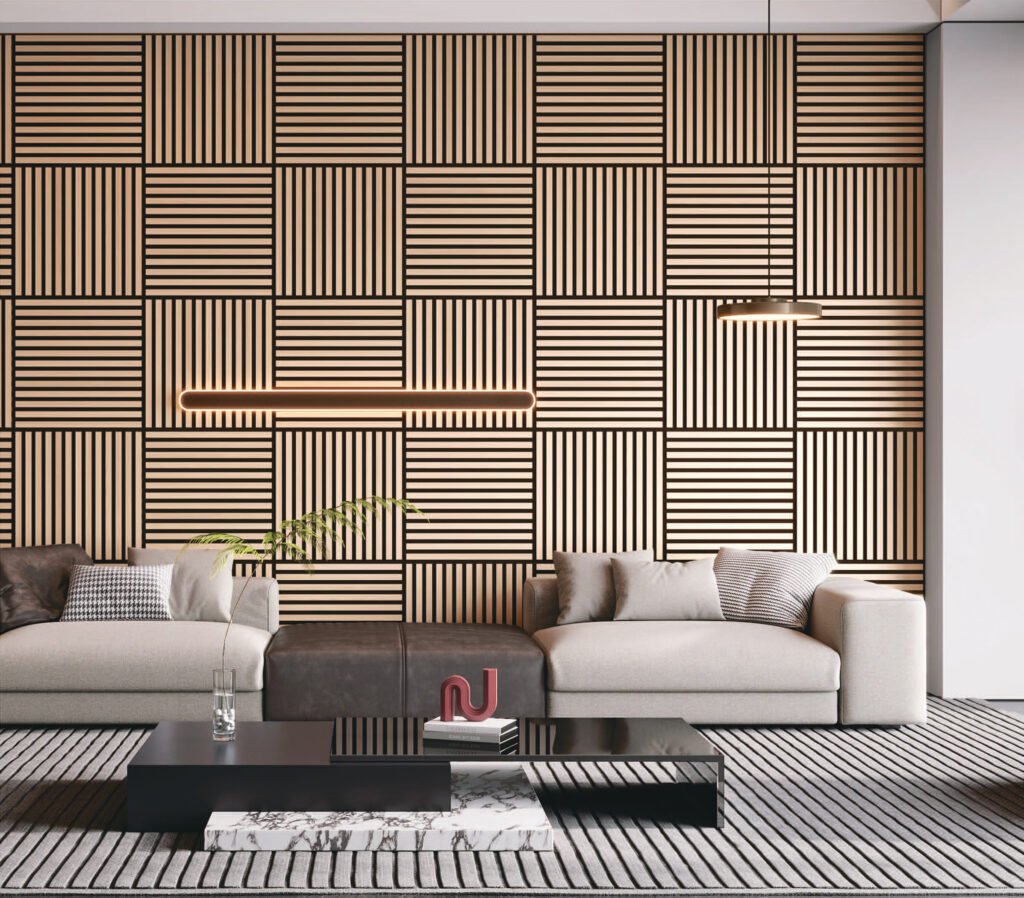
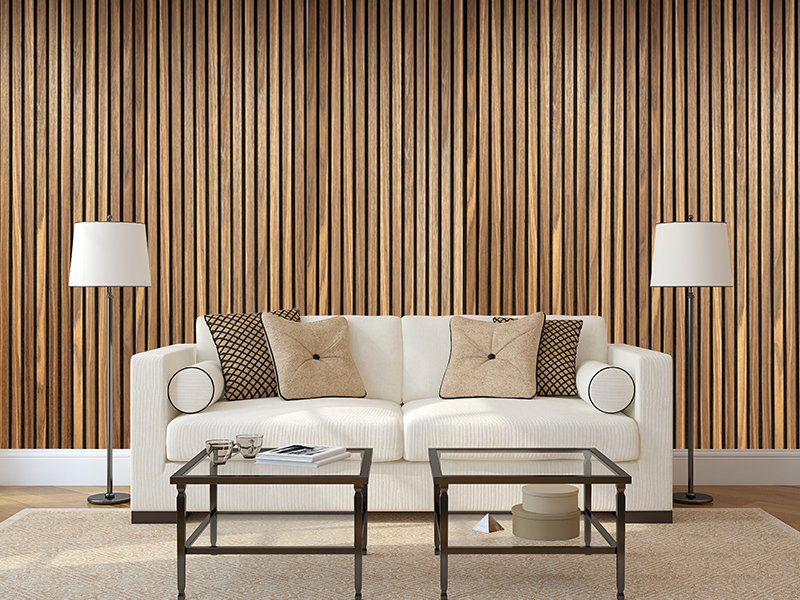
Raw Materials Sourcing
The production of acoustic wall panels begins with selecting the best materials. There are two main types of materials commonly used in acoustic panels: PET (Polyethylene Terephthalate) and MDF (Medium Density Fiberboard).
PET : Made from recycled plastic bottles, PET panels are eco-friendly, lightweight, and offer excellent sound absorption. PET is an ideal choice for creative designs due to its versatility and sustainable nature.
MDF : MDF is known for its durability, strength, and ability to support a range of surface finishes. It is often used in high-end designs and more structural panel applications.
Both materials are sourced from trusted suppliers that meet international quality standards, ensuring the durability and performance of every panel.
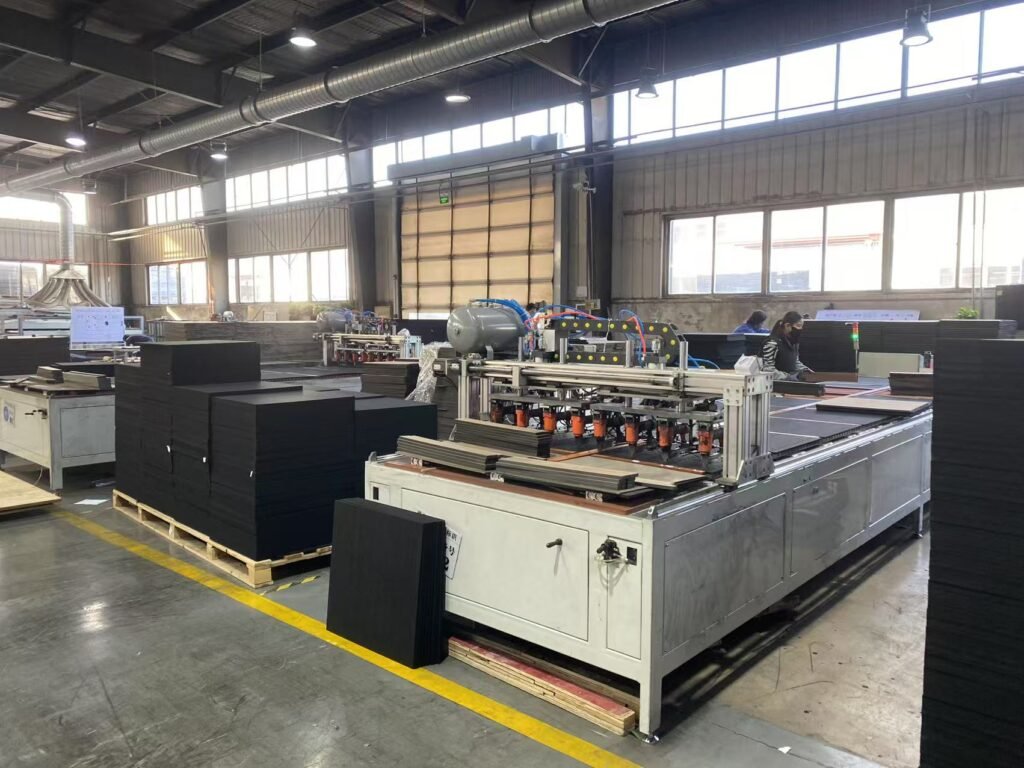
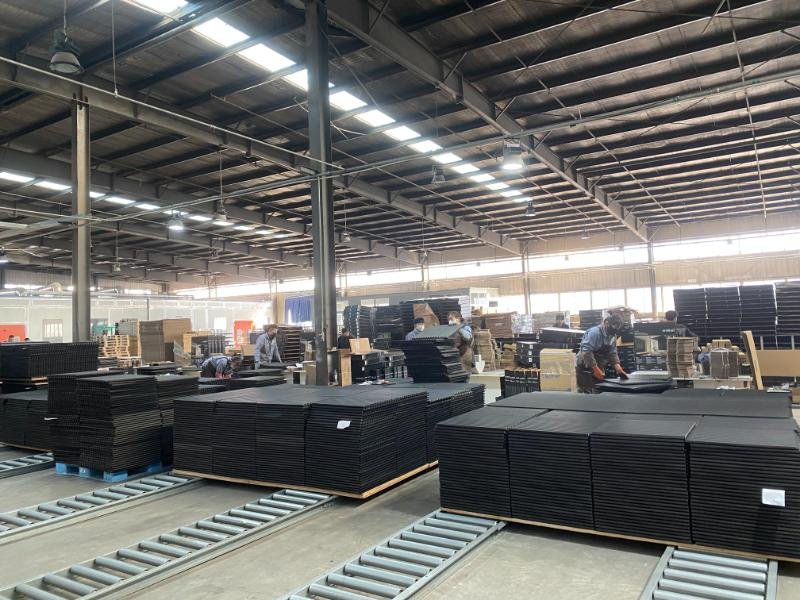
Surface Treatment Options
Once the basic panel is formed, various surface treatments are applied. These treatments not only enhance the visual appeal but also contribute to the panel’s performance in sound absorption.
–Technical wood veneer
–PVC veneer
–Wood Veneer: For a more luxurious appearance, panels may be finished with wood veneer, offering an elegant and natural look.
At MasterWallPro, we offer a variety of surface treatments tailored to meet the needs of our customers.
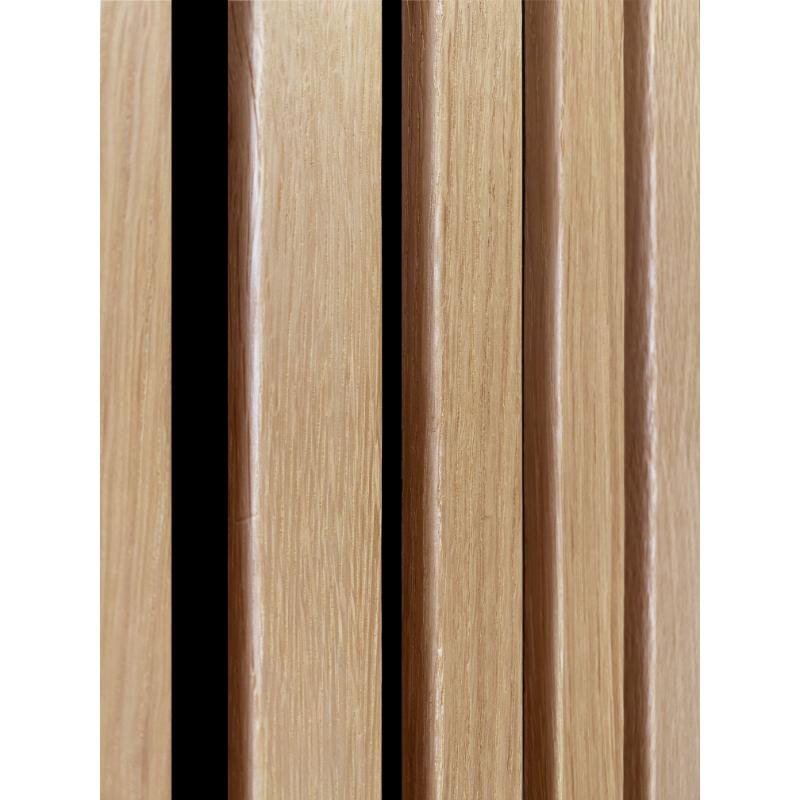
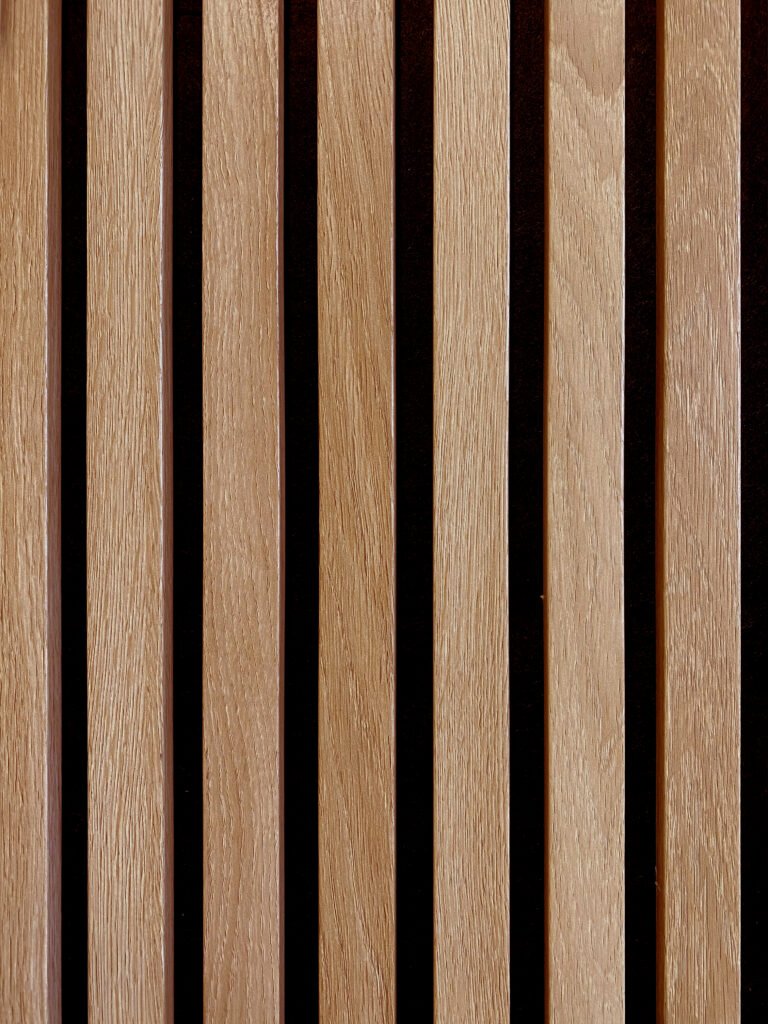
Quality Control and Testing
Quality control is a critical part of the manufacturing process. Each batch of acoustic panels undergoes rigorous testing to ensure they meet the highest standards of sound absorption, fire resistance, and durability.
Sound Absorption Testing: Panels are tested for their NRC (Noise Reduction Coefficient) rating, ensuring they perform effectively in reducing noise levels.
Fire Resistance: We test our panels for fire resistance to ensure they meet global safety standards.
Durability Testing: Panels undergo scratch resistance and moisture exposure tests to ensure they can withstand various environmental conditions.
This strict quality control process guarantees that every panel leaving the factory performs as expected.
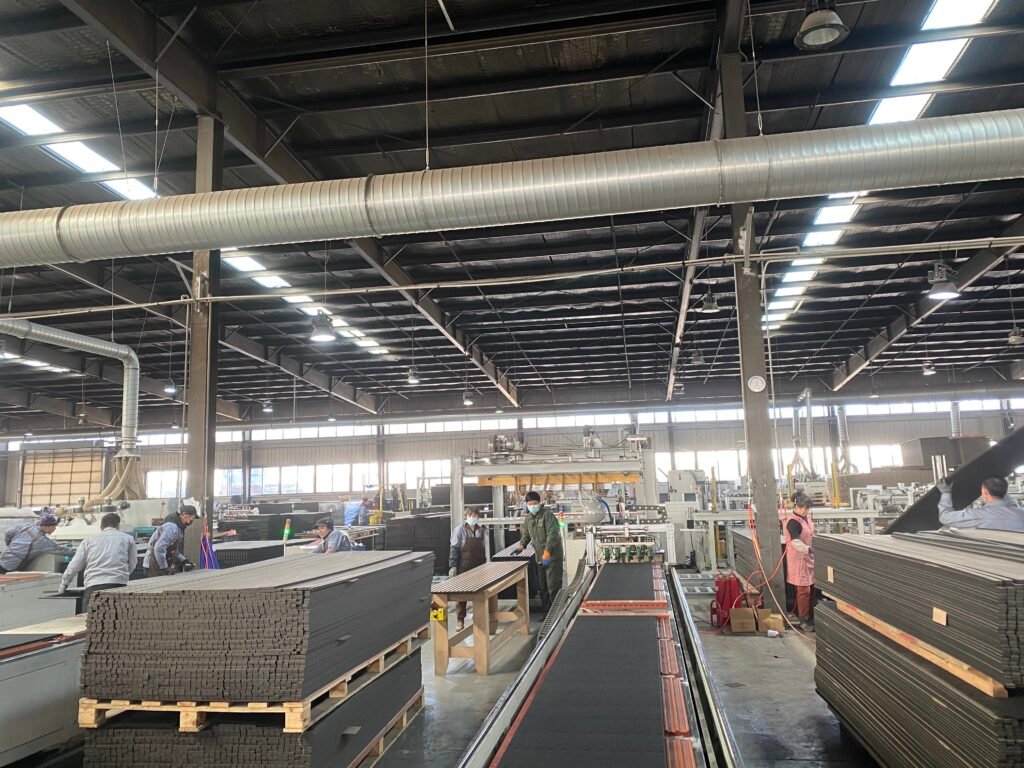
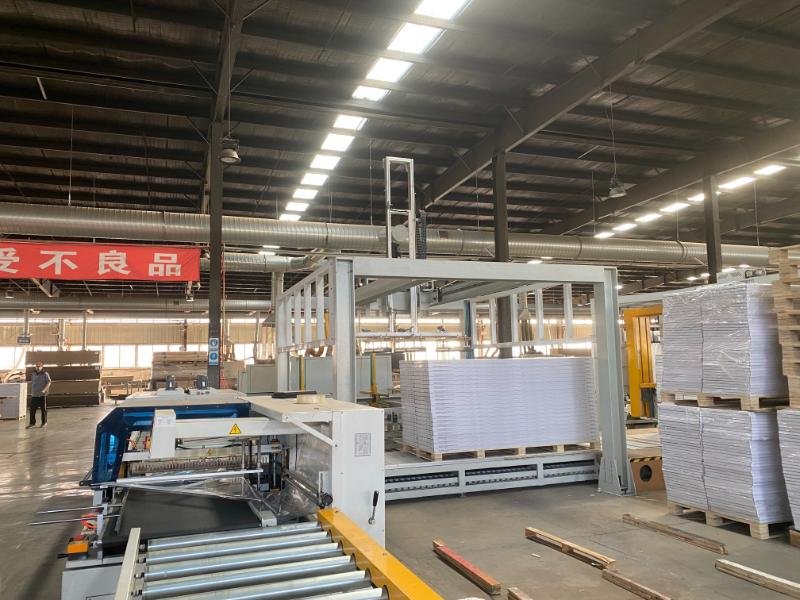
MasterWallPro Factory Strengths
At MasterWallPro, we pride ourselves on our state-of-the-art manufacturing facilities located in China and Vietnam. Our factories are equipped with the latest technology, allowing us to produce high-quality acoustic wall panels efficiently and at scale. Here are some of the strengths of our factory:
Advanced Production Line: Our production line is designed to maximize efficiency while maintaining the highest standards of quality.
Customizability: We offer a wide range of customization options, including sizes, finishes, and surface treatments, ensuring every project gets exactly what it needs.
Fast Turnaround Times: With our streamlined processes and large-scale production capabilities, we can meet tight deadlines without compromising on quality.
We’ve worked with clients across various industries, including commercial, residential, and hospitality, helping them achieve superior soundproofing solutions that enhance their spaces.
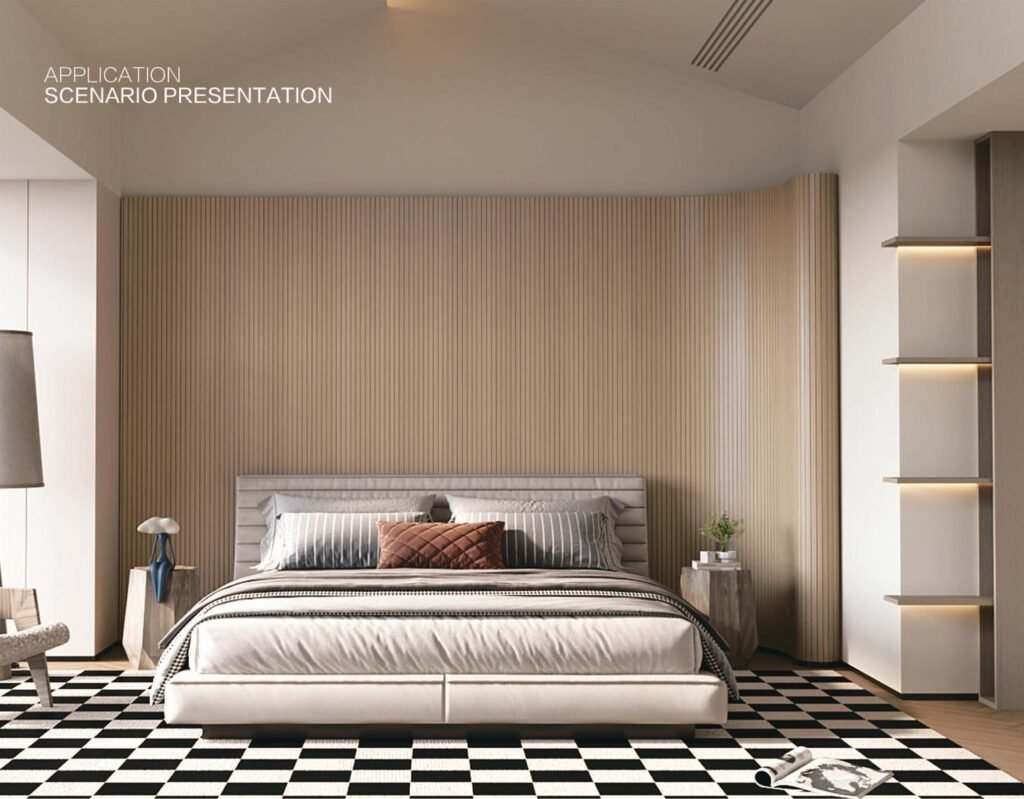
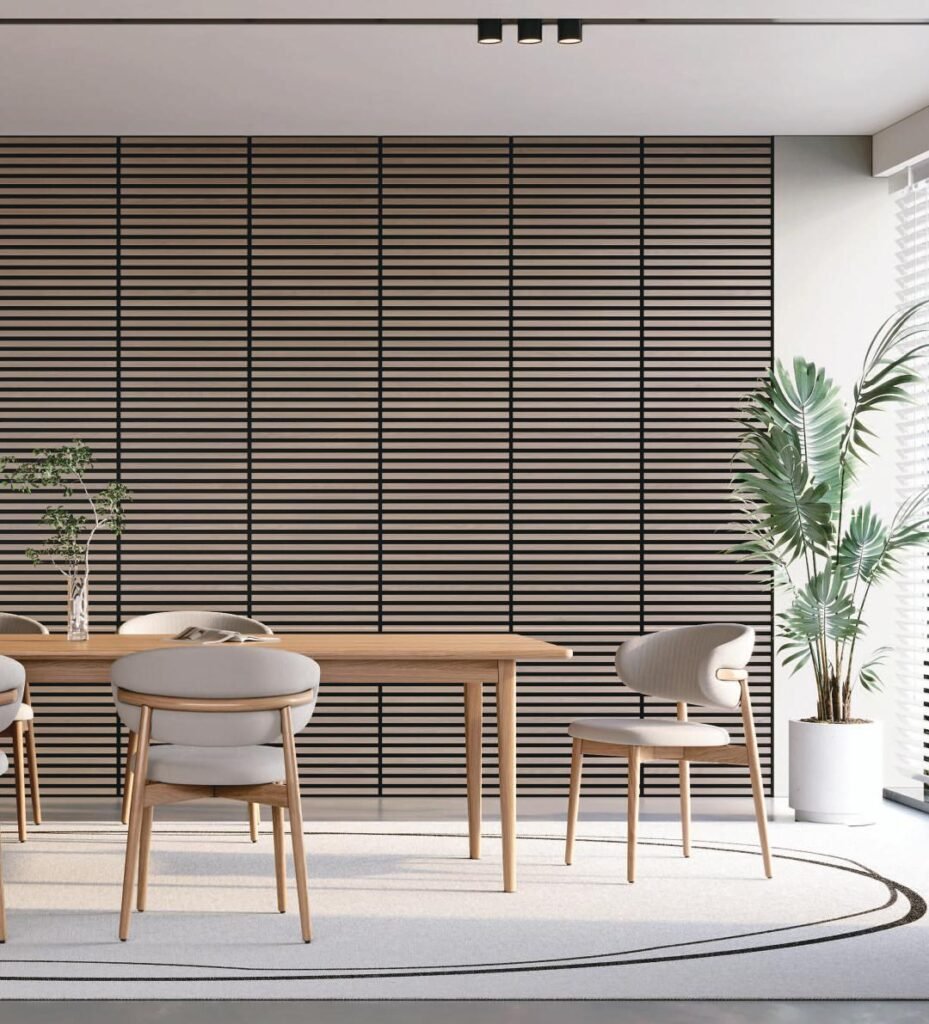